For a long time, electroplating dominated the surface treatment of automotive components due to its strong adhesion, metallic finish, and relatively mature production process. It was widely used on interior and exterior trims, door handles, emblems, grilles, and more, becoming almost synonymous with "metallic finish." It provided a stable and low-barrier solution for many component suppliers.
However, entering the new energy vehicle (NEV) era, application demands have surged. Coupled with stricter national environmental policies and the automotive industry's heightened requirements for material eco-friendliness, process cleanliness, and functional coatings, this traditional process is now facing criticism. Furthermore, the large-scale production demands of NEVs pose severe challenges to the response speed and efficiency levels of traditional electroplating lines. Under these converging pressures, a clear reality emerges: electroplating's golden age is over, and its phase-out is underway.
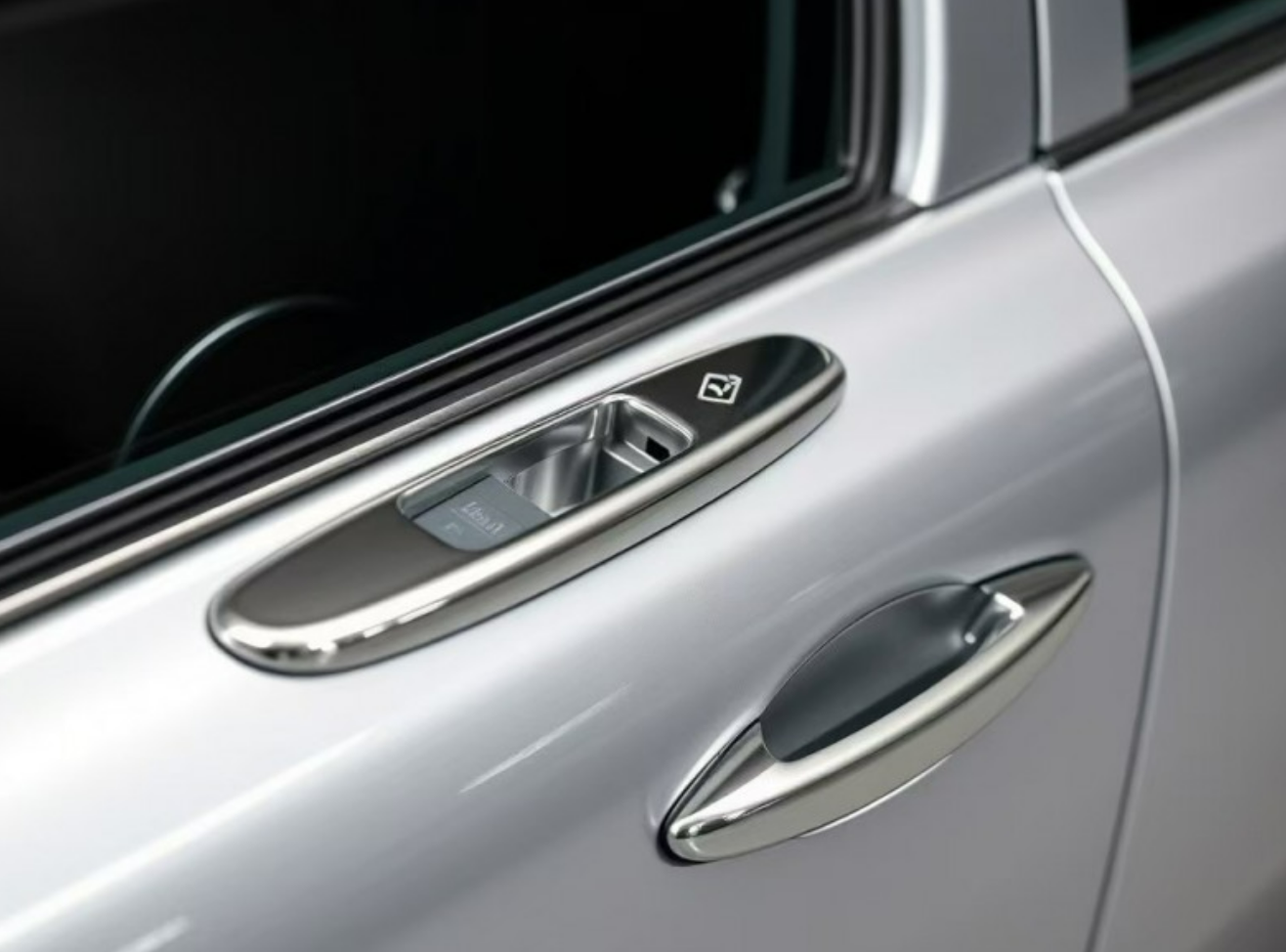
Why is Electroplating Being "Phased Out"? The Real Dilemma Under Triple Pressures
1. Policy Pressure: Environmental Red Lines Tighten, Electroplating Enters High-Risk Zone
Against the backdrop of advancing "Dual Carbon" goals, the electroplating industry is a key focus of environmental regulation. Strict monitoring now covers wastewater discharge, heavy metal ions, acid/alkali exhaust gases, etc., leaving almost zero room for error. Under this pressure, companies must bear high compliance costs for upgrading environmental facilities, installing online pollution monitoring, and managing hazardous waste disposal, continuously squeezing profit margins. Simultaneously, the risk of a "one-strike policy" shutdown is prominent – minor oversights can lead to production restrictions, suspensions, or even broken capital chains. Moreover, electroplating suppliers lacking environmental credentials or failing emissions audits are being progressively eliminated from OEM supply chains. Markets like Europe and the US also impose environmental barriers (RoHS, REACH, ELV) on electroplated products. The supply chain is greening rapidly, further constricting business survival space.
2. Technical Bottlenecks: Difficulty Balancing Functionality and Lightweighting
Current electroplating primarily enhances aesthetics and corrosion resistance, struggling to meet NEVs' integrated demands for lightweighting, multi-material use, and electronic functionality. In harsh environments (high heat, strong light), electroplated coatings are prone to discoloration and cracking. Their compatibility with plastics, composites, and components requiring light transmission or sensing functions is poor. Achieving high yields on complex structures or multi-layer precision coatings is also challenging. These technical limitations significantly hinder electroplating companies from expanding into the NEV market.
3. Capacity Bottleneck: Struggling with High-Tempo Production
With the continuous growth in NEV production and sales, OEMs demand greater flexibility from component suppliers. According to the China Association of Automobile Manufacturers, China's NEV output/sales exceeded 9.5 million units in 2024, a YoY increase of approximately 30.3%. OEM "daily scheduling" rhythms are accelerating. However, electroplating's long cycle times, inconsistent batch quality, and constraints from environmental approvals and production permits make it difficult to meet demands for large-scale, high-tempo, high-consistency production. Supply chain adaptability is clearly insufficient, making industry transformation urgent.
Why is PVD Taking the Baton? Cleaner, More Advanced, More Future-Oriented
Just as electroplating enters its "high-risk zone," green coating technologies like PVD (Physical Vapor Deposition) are increasingly seen by automakers as the future for surface treatment of interior and exterior trims.
PVD is a physical process conducted in a vacuum, depositing metal materials onto substrates via evaporation or sputtering. It doesn't rely on heavy-metal-containing electrolytes, offering a clean process, dense coating structure, and strong adhesion. PVD coatings provide excellent aesthetics alongside superior mechanical properties and corrosion resistance.
Compared to traditional electroplating, PVD holds systemic advantages in performance and manufacturing flexibility:
* Enables multi-layer coating designs for combined decorative and functional requirements.
* Applicable to diverse substrates and complex structural parts.
* Supports customization of various coating materials and colors.
* Features fast cycle times and high efficiency, better suited for flexible manufacturing models.
Industry estimates indicate over 60% of mainstream passenger car brands now use PVD on their premium or NEV models, including BYD, NIO, Li Auto, Volkswagen, and BMW. PVD is evolving from an emerging technology towards an industry standard. To further enhance coating performance, PVD is often combined with CVD (Chemical Vapor Deposition) to form composite structures. A CVD transparent protective topcoat can significantly boost corrosion resistance and color stability. However, traditionally separate PVD and CVD steps suffer from low efficiency and yield fluctuations. Consequently, some equipment manufacturers are accelerating R&D and application of integrated PVD-CVD process equipment to improve overall efficiency and production line consistency.
Currently, PVD technology is rapidly scaling up from niche applications. Multiple industry forces are collaborating to drive process integration and production line upgrades:
* **Equipment:** Companies like Zhenhua Vacuum have launched integrated automotive interior coating equipment capable of depositing the metal layer and forming the protective topcoat in a single loading step.
* **Processing:** Companies like Jinzhong Auto Parts and Chuzhou Jiamei Precision Industry are actively deploying PVD applications.
* **OEMs:** Brands like Li Auto, BYD, and NIO have achieved batch adoption in mid-to-high-end models, shifting PVD from "optional" towards "standard."
For interior component manufacturers who transition to PVD early, this upgrade brings not only process optimization but also enhanced operational resilience and market competitiveness. High-consistency coating quality reduces rework rates and quality control pressure. Customizable, multi-color coating options increase product value. Green compliance credentials also allow companies to navigate export regulations and OEM green supply chain assessments more confidently, winning more cooperation opportunities and brand recognition.
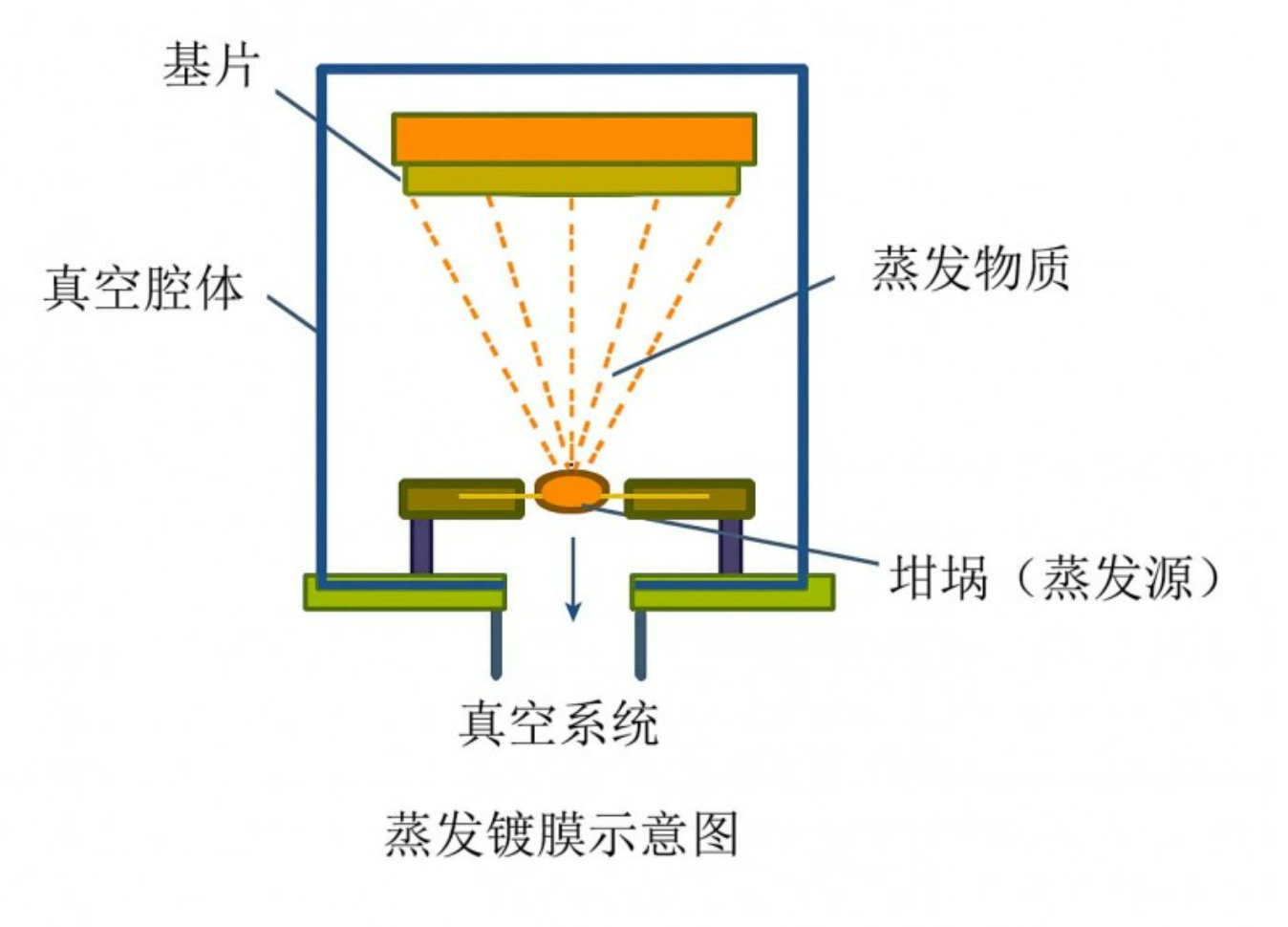
Conclusion: PVD Isn't Just "Replacement," It's the Starting Point for Industry Transformation
Clearly, electroplating's "glory days" are irreversibly ending. PVD is more than just an eco-friendly alternative; it is a "critical process pivot" for the automotive industry's future. Under the trends of electrification, intelligence, and lightweighting, OEMs have elevated "green manufacturing" to a core strategy. Whether component suppliers possess the capability for environmentally friendly, efficient, functional coating manufacturing will directly determine their long-term partnerships and role in the next decade's industrial competition. Facing this tide of change, companies bold enough to invest and decisively transform stand at the starting line of a new competitive landscape. Hesitation and delay will only mean missing the future.
PVD represents not just an innovation in coating technology, but a deeper transformation in automotive manufacturing itself.